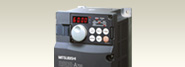
Mitsubishi inverter FR-A700
The control methods of Mitsubishi inverter are mainly divided into: V/f control, including open loop and closed loop; vector control , including speed sensor and speed sensor control; direct torque control; the advantages and disadvantages of the three methods are as follows: (1) V / f open loop control < advantages:="" simple="" structure,="" easy="" adjustment,="" available="" for="" general-purpose="" squirrel-cage="" asynchronous="" motor;="">
Disadvantages: low-speed torque is difficult to guarantee, torque control cannot be adopted, and the speed regulation range is small;
Mainly used occasions: general fan, pump energy-saving speed regulation or one frequency conversion With multiple motor drive applications. (2) V/f closed-loop control. Advantages: simple structure, high speed regulation accuracy, can be used for general-purpose asynchronous motors; disadvantages: low-speed torque is difficult to guarantee, and torque control cannot be used. The speed adjustment range is small, and the speed sensor should be added;
Mainly used occasions: used to maintain pressure, temperature, flow rate, PH setting and other process occasions. (3) Vector control without speed sensor Advantages: no speed sensor is required, torque response is good, structure is simple, and speed control range is wide;
Disadvantages: motor parameters need to be set, There are automatic test functions;
Use occasions: general industrial equipment, most speed control occasions. (4) Vector control with speed sensor Advantages: good torque control performance, good torque response, high speed regulation, and large speed control range;
Disadvantages: need to set the motor correctly Parameters, automatic test function required, high precision speed sensor; use occasion: high dynamic performance applications requiring precise control of torque and speed. (5) Direct torque control Advantages: no speed sensor is required, torque response is good, structure is simple, and speed control range is large;
Disadvantages: motor parameters need to be set, Automatic test function;
Use case: High dynamic performance applications requiring precise control of torque, such as cranes, elevators, rolling mills, etc.